ED1-2 timer production and sales process
Shuangyang Group is a high-tech enterprise that integrates R&D, production and sales. The company has a complete management system, so after the company's sales clerk receives the customer's ED1-2 order, multiple departments need to cooperate to complete the order production.
Planning Department
Conduct price review, and the merchandiser will input product quantity, price, packaging method, delivery date and other information into the ERP system
Review department
After passing the review of multiple parts, it will be sent to the production department by the system.
Production department
The production department planner develops the master production plan and material requirements plan based on the sales order, and passes them to the production workshop and purchasing department.
Purchasing Department
Supply copper parts, electronic components, packaging, etc. according to planned requirements, and arrange production in the workshop.
Production Process
After receiving the production plan, the production workshop instructs the material clerk to pick up the materials and schedule the production line. The production process of ED1-2 timer mainly includes injection molding, silk screen printing, riveting, welding, complete machine assembly, packaging and other processes.
Injection molding process:
According to the process requirements, an injection molding machine is used to process the PC material into plastic parts such as timer housings and safety sheets.
Silk screen printing process:
According to certification and customer requirements, ink is printed on the timer housing, including customer trademarks, function key names, voltage and current parameters, etc.
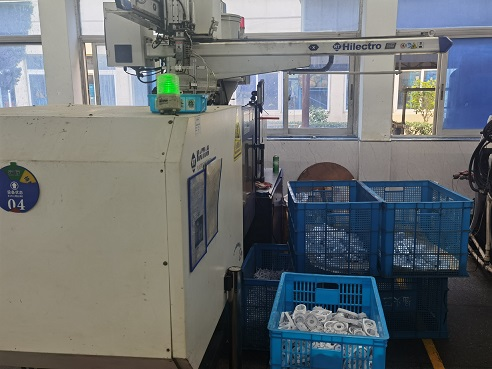
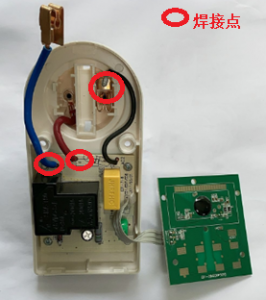
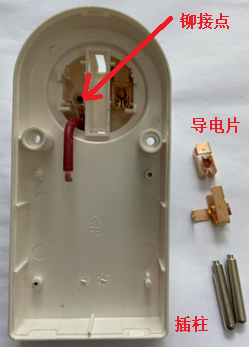
Riveting process:
Put the plug into the plug hole of the housing, install the conductive piece on the plug, and then use a punch to punch the two together. When riveting, the stamping pressure must be controlled to avoid damaging the shell or deforming the conductive sheet.
Welding process:
Use solder wire to weld the wires between the conductive sheet and the circuit board. The welding must be firm, the copper wire should not be exposed, and the solder residue must be removed.
Injection molding process:
According to the process requirements, an injection molding machine is used to process the PC material into plastic parts such as timer housings and safety sheets.
Silk screen printing process:
According to certification and customer requirements, ink is printed on the timer housing, including customer trademarks, function key names, voltage and current parameters, etc.

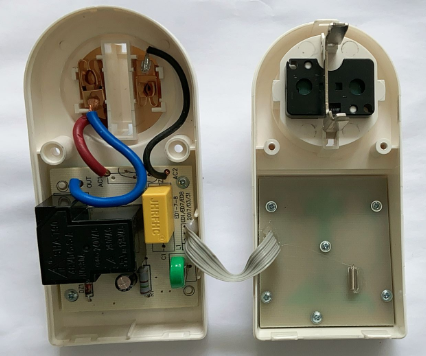
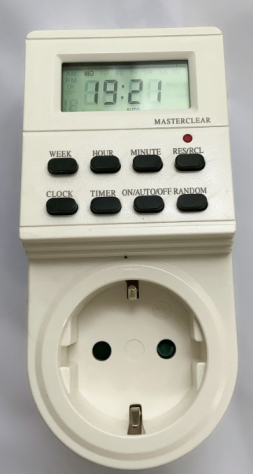
Inspection Process
ED1-2 timers conducts product inspection at the same time as production. The inspection methods are divided into first article inspection, inspection and finished product inspection.
In order to discover factors that affect product quality during the production process of digital weekly timers as early as possible and prevent batch defects or scrapping, the first product of the same batch is inspected for appearance and performance, including inspection items and finished product inspection.
Main inspection items and judgment standards.
Main inspection items and judgment standards.
Output performance
Place the product on the test bench, turn on the power and plug in the output indicator light. It must be clearly on and off. There is output when "ON" and no output when "OFF".
Timing function
Set 8 sets of timer switches, with switching actions at intervals of 1 minute. The timer can make switching actions according to the setting requirements
Electrical strength
The live body, ground terminal, and shell can withstand 3300V/50HZ/2S without flashover or breakdown
Reset function
When pressed, all data can be cleared normally and timing starts from the system default settings
Travel time function
After 20 hours of operation, the travel time error does not exceed ±1min
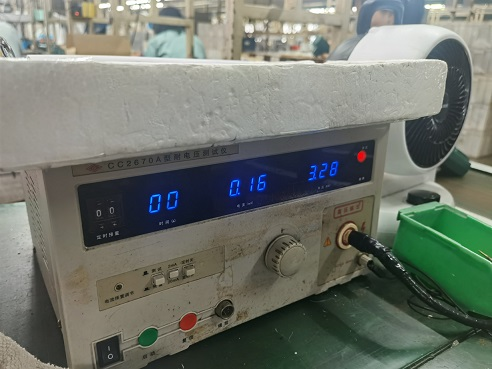
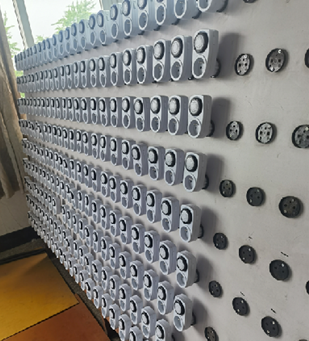
After the finished product inspection is completed, the workshop carries out product packaging, including labeling, placing paper cards and instructions, placing blister or heat shrink bags, loading inner and outer boxes, etc., and then placing the packaging boxes on wooden pallets. The inspectors from the Quality Assurance Department check whether the product model, quantity, paper card label content, outer box mark and other packaging in the carton meet the requirements. After passing the inspection, the product is put into storage.
Sales, Delivery and Service
As a R&D technology factory with 38 years of industry experience, we have a complete sales and after-sales system to ensure that customers can receive timely technical support and quality assurance after purchasing digital timers and other products.
Sales and shipment
The sales department determines the final delivery date with the customer based on the production completion status, fills out the "Delivery Notice" on the OA system, and contacts the freight forwarding company to arrange container pickup. The warehouse manager checks the order number, product model, shipment quantity and other information on the "Delivery Notice" and handles the outbound procedures.
Export products such as one-week mechanical timers are transported by the freight forwarding company to the Ningbo Port terminal for warehousing, waiting for container loading. The land transportation of the products is completed, and the sea transportation is the responsibility of the customer.
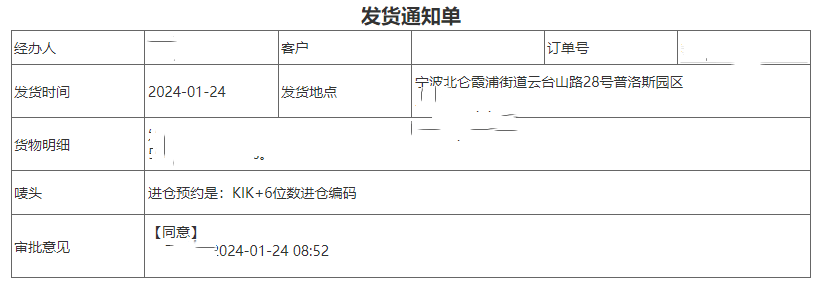
After-sales service
If the products provided by our company cause customer dissatisfaction due to quantity, quality, packaging and other issues, and the customer gives feedback or requests a return through written complaints, telephone complaints, etc., each department will implement the "Customer Complaints and Returns Handling Procedures".
When the returned quantity ≤ 3‰ of the shipment quantity, the delivery staff will transport the products requested by the customer back to the company, and the salesperson will fill in the "Return and Exchange Processing Flow Form", which will be confirmed by the sales manager and analyzed by the quality assurance department based on the reason. The Vice President of Production will approve the replacement or rework.
When the returned quantity is greater than 3‰ of the shipped quantity, or when the inventory is overstocked due to order cancellation, the salesperson fills out the "Batch Return Approval Form", which is reviewed by the sales department supervisor, and the general manager ultimately decides whether to return the goods.
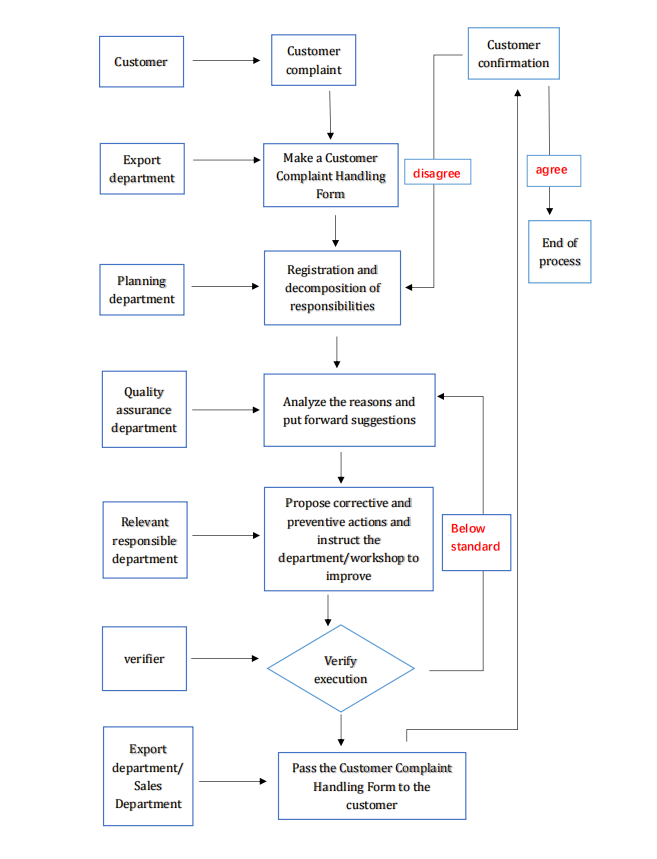
The sales clerk accepts customer complaints, fills in the description of the user complaint problem in the "Customer Complaint Handling Form", and passes it to the planning department after review by the sales department manager.
After the planning department confirms, the quality assurance department will analyze the reasons and make suggestions.
The planning department decomposes responsibilities based on the cause analysis and suggestions and passes them to relevant departments. The heads of relevant responsible departments propose corrective and preventive measures and instruct their departments/workshops to improve.
The verification personnel check the implementation status and feedback the information to the planning department, and the planning department passes the original "Customer Complaint Handling Form" to the import and export department and sales department.
The export department and sales department will feedback the processing results to customers.
Enterprise strength
Development History
Shuangyang Group was established in 1986. In 1998, it was rated as one of Ningbo Star Enterprises and passed ISO9001/14000/18000 quality system certification.
Factory area
The actual factory of Shuangyang Group covers an area of 120,000 square meters, with a construction area of 85,000 square meters.
Serving officers
Currently, the company has more than 130 employees, including 10 high-end technology R&D engineers and more than 100 QC personnel to ensure the quality of mechanical timers and other products.
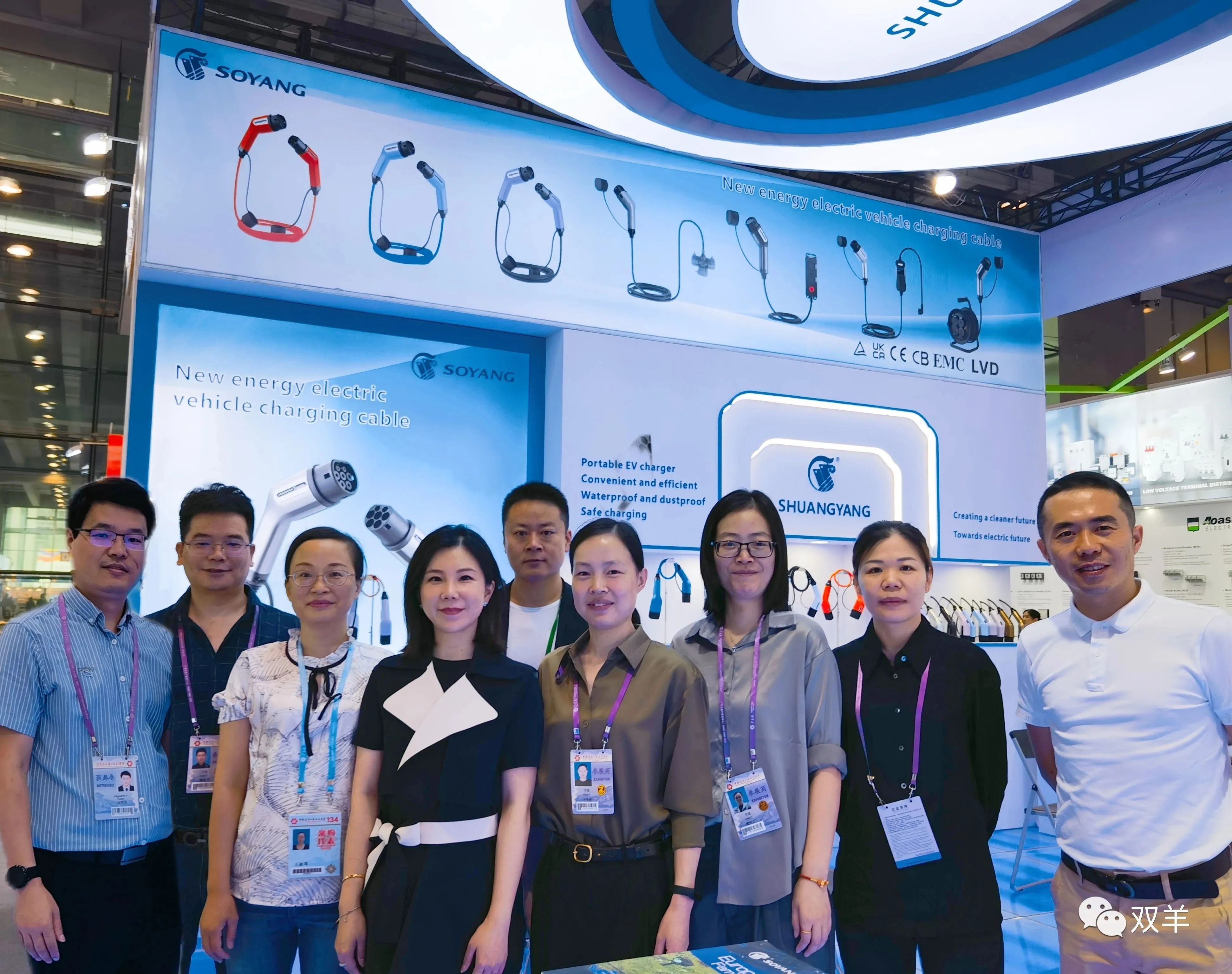
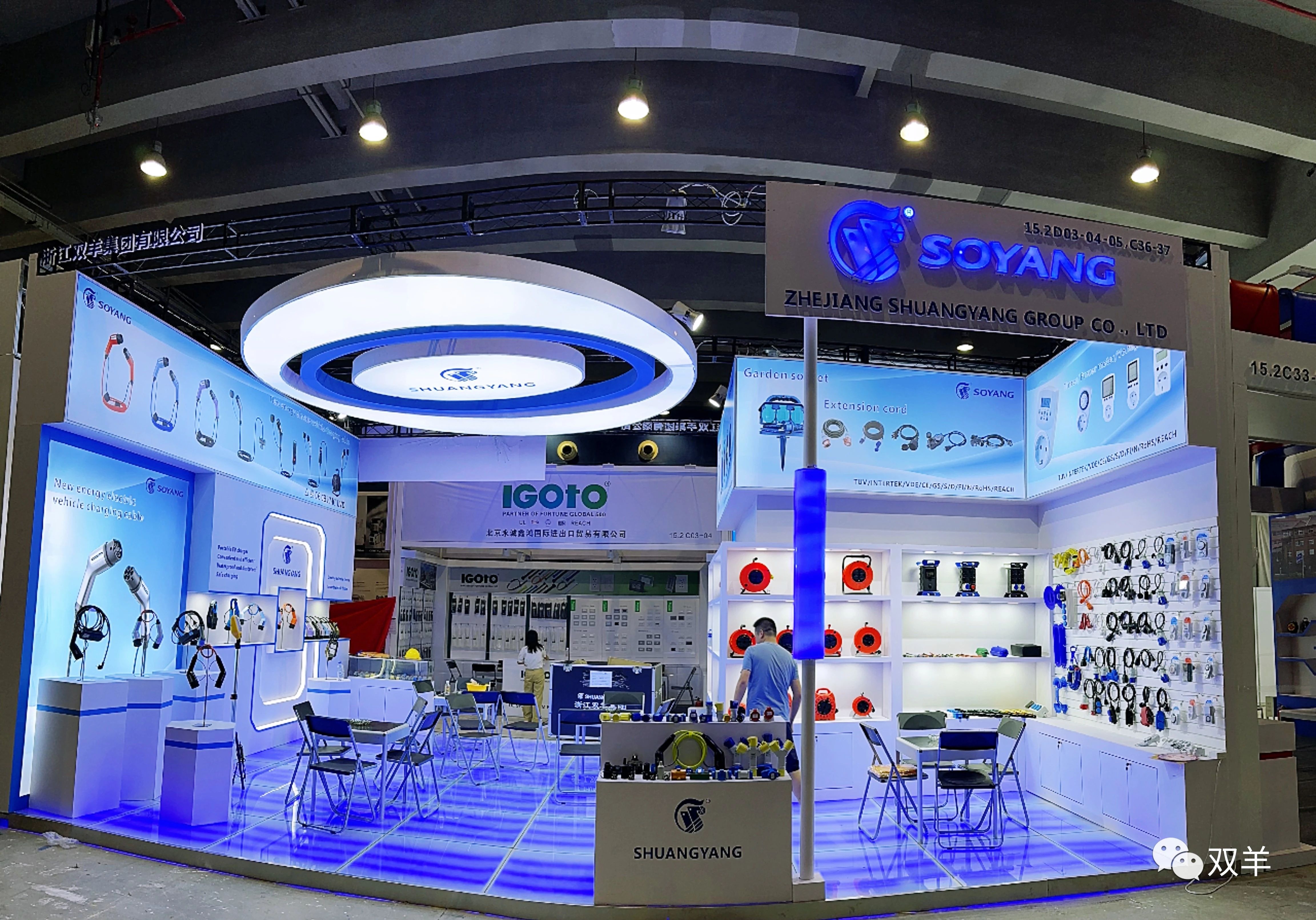
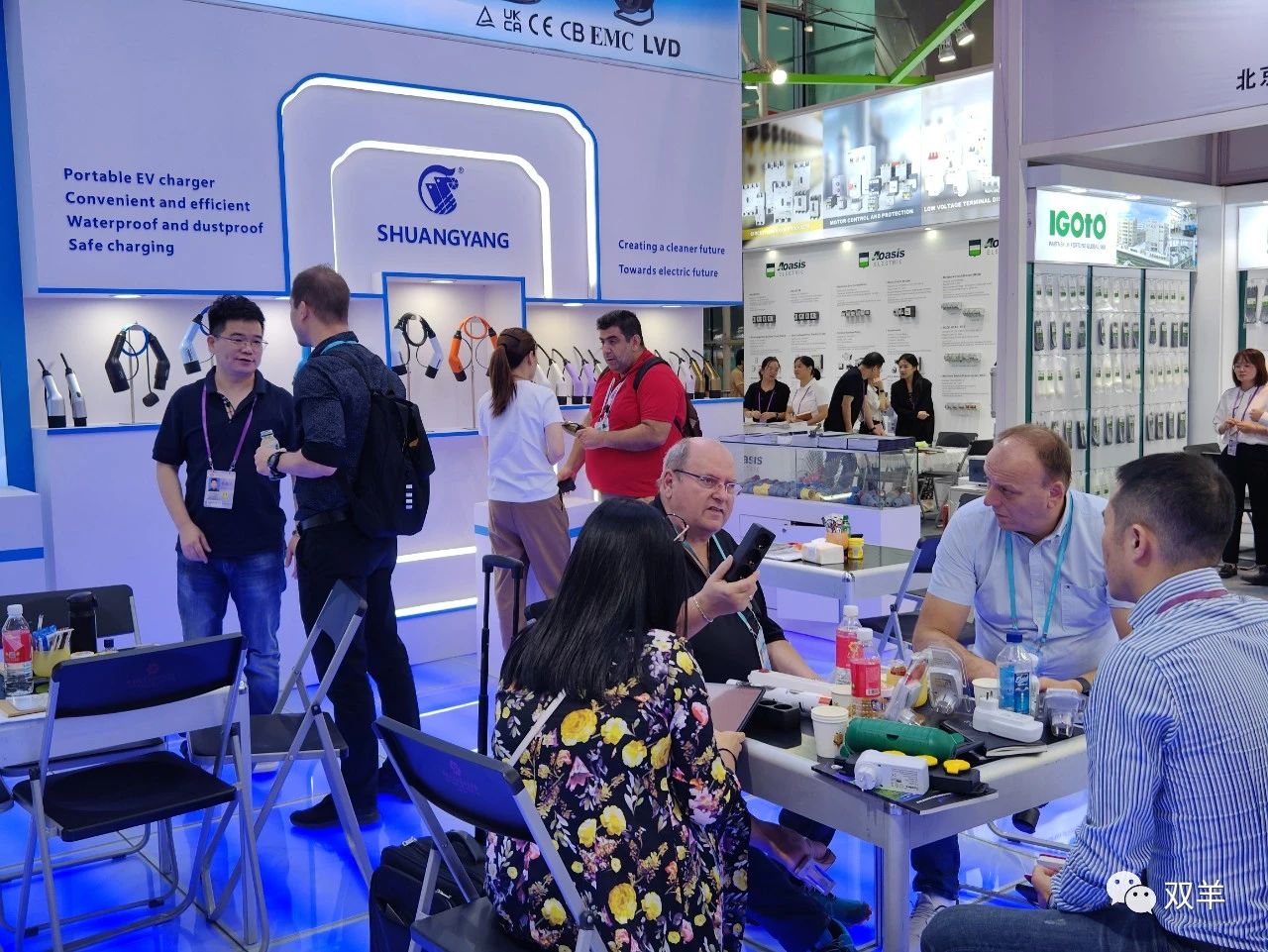